The Micro Autonomous Underwater Vehicle (μAUV) was developed and built as a demonstrator for the Hannover trade show in just two months [1,2]. In [1] we describe the design and development of such a small autonomous underwater vehicle. The main body of the μAUV has a cylindrical shape with a diameter of 55mm and a length of 125mm. Two horizontal thrusters, two vertical thrusters and one thruster for the lateral movements (Fig. 1a) are attached to the upper part of the vehicle. This arrangemant makes it possible to hover in any direction. The batteries are mounted outside in two tubes attached to the lower part of the vehicle providing a very low center of gravity. Thus resulting in a stable standing position while the vehicle is aquatic. We optimized the design to achieve a very short production time. Building a robot as an underwater vehicle requires a lot of special knowledge in materials and sealing. For the μAUV we use polypropylene with a density of 0.92 g/cm³. Thus the material itself has positive buoyancy, which is essential when building an underwater vehicle with such small dimensions. In addition, polypropylene has no hygroscopicity.
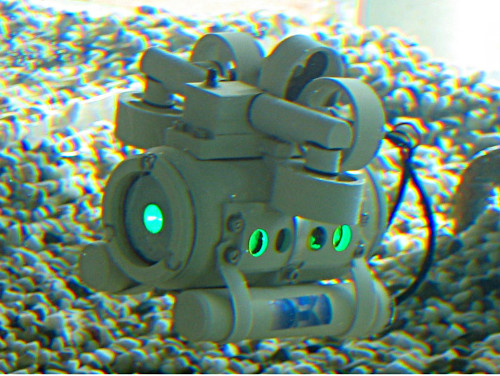
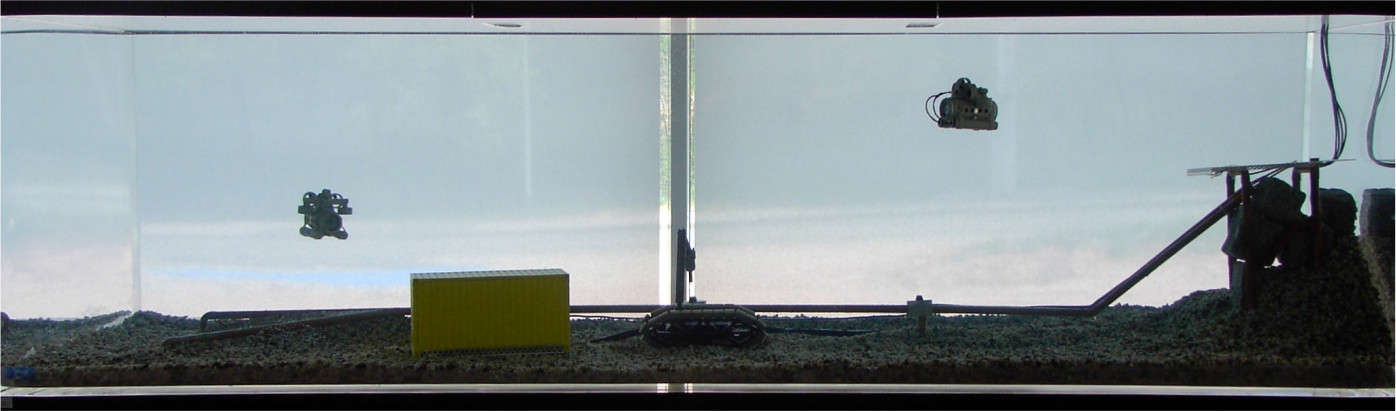
Due to the size and weight constraints imposed by the dimensions of the vehicle the design of the μAUV electronics was a challenging task. The electronics of our μAUV consists of a main-board, eight sensor-boards and a pressure sensor directly integrated into the hull. The mainboard is equipped with an Atmel ATMega128 microcontroller, two L298 dual full-bridge drivers and a ULN2803 darlington array. The eight sensor-boards are each equipped with a green SuperFlux LED by Lumileds Lighting and up to four RGB light sensors TCS230 by TAOS. The ATMega128 is an 8-bit microcontroller with 128KB flash memory and 4KB SRAM. The chip generates the PWM signals for motor control, measures the 12 light sensors and the pressure sensor and controls the movements of the vehicle via a behaviour based approach. To coordinate these different tasks on the microcontroller a very lightweight non-preemptive scheduler was implemented.
The μAUV relies on two types of sensors. A pressure sensor which measures the differential pressure between the inside and outside of the vehicle and eight RGB light-to-frequency sensors which measure the intensity of red, green and blue light at different locations on the vehicle. The differential pressure between inside and outside of the vehicle is used to estimate the depth of the vehicle. For every centimeter in depth the pressure rises by 1 hectopascal. The pressure outside of the vehicle is not only affected by the pressure originated by the water column above the vehicle, it is also affected by the atmospheric pressure at water level. As the pressure inside the vehicle is constant after it is sealed, pressure changes in the atmosphere influence the estimation of the vehicle’s depth. The difference between a high-pressure area and a low-pressure area is around 30 hectopascal or about 30 centimeter in terms of the depth estimation. For this reason the μAUV periodically recalibrates the minimum and maximum sensor values by surfacing to water level for the minimum pressure value and descending to the ground for the maximum pressure value. The eight RGB light-to-frequency sensors which are distributed over different locations on the vehicle measure the light intensity of red, green and blue light at their particular positions. The sensors generate a square wave whose frequency is proportional to the intensity of light measured. One of the sensors main purposes is obstacle detection. To detect an obstacle, the green light intensity is measured before and during a green LED pointing outwards is turned on. If an obstacle is near it reflects the green light and a significant increase in the green light intensity can be detected.
The μAUV have been successfully used as demonstrators over the complete duration of this years CeBIT fair in Hannover/Germany. We used four different systems with two systems in the water and two systems being recharged. The hardware of the system worked reliable and all systems were still running after one week of daily eight hours of demonstration. At the end of the week we noticed a certain amount of corrosion in the motors and around the power connectors as a direct result of electrolysis. The runtime of a battery charge was around two and a half hours.
References
1
,
Design of a μAUV,
In: Proceedings of the 4th International AMiRE Symposium (AMiRE-2007). Buenos Aires, Argentinien: Heinz Nixdorf Institut Universiät Paderborn, pp. 99–106, 2007,
[pdf|bibtex]
best paper award
2
,
Sensor Processing and Behaviour Control of a Small AUV,
In: Autonome Mobile Systeme AMS 2007- 20. Fachgespräch Kaiserslautern. Robotics Research Lab of the University of Kaiserslautern. Kaiserslautern, Germany: Springer, pp. 327–333, 2007,
[pdf|doi|bibtex]